2013年4月,德國首提“工業(ye) 4.0”戰略。2019年2月5日,德國正式發布《國家工業(ye) 戰略2030》,明確提出在某些領域德國需要擁有國家及歐洲範圍的旗艦企業(ye) 。以下文章轉自智能論壇公眾(zhong) 號,由天拓四方推薦閱讀。
兩(liang) 天之後,2019年2月7日,美國發布了由總統特朗普親(qin) 自主持製定的未來工業(ye) 發展規劃,將人工智能、先進的製造業(ye) 技術、量子信息科學和5G技術列為(wei) “推動美國繁榮和保護國家安全”的四項關(guan) 鍵技術。在白宮官網上,這份規劃的標題是——“美國將主宰未來工業(ye) ”。
2019年4月11日,日本政府概要發布了2018年度版《製造業(ye) 白皮書(shu) 》,指出在生產(chan) 第一線的數字化方麵,中小企業(ye) 與(yu) 大企業(ye) 相比有落後傾(qing) 向,應充分利用人工智能的發展成果,加快技術傳(chuan) 承和節省勞力。
今天,距離第一次提出“工業(ye) 4.0”戰略已經六年了。當前大國間的製造業(ye) 競賽如火如荼。第四次工業(ye) 革命正在以前所未見的速度迎麵撲來,突破性技術和創新型業(ye) 態催生的強大力量,將改寫(xie) 全球製造業(ye) 的競爭(zheng) 格局。
這是最好的時代。中國迎來了智能製造發展的破局時刻。作為(wei) 先進製造業(ye) 後來者,中國製造正在以中國速度和中國智慧奮力追趕,以期實現高質量發展,由大變強,後發先至。
想到+做到=得到
態度決(jue) 定行動,行動決(jue) 定結果,想到+做到=得到,這就是中國智能製造成功破局的公式。
想到:中國企業(ye) 對第四次工業(ye) 革命滿懷信心,對投身智能製造樂(le) 觀而不遲疑
2016年和2017年,麥肯錫連續兩(liang) 次對中美德日四國400多家企業(ye) 領袖進行了智能製造問卷調研,麵對同樣一個(ge) 問題:“與(yu) 一年前相比,你對智能製造潛力的態度有何變化?”(見圖1)結果顯示,中國企業(ye) 對智能製造抱有極大的熱情和期待,遠比美德日企業(ye) 樂(le) 觀:86%的中國受訪企業(ye) 相信智能製造的潛在價(jia) 值,比例遠高於(yu) 美德日三個(ge) 發達經濟體(ti) 的企業(ye) (美國67%,德國62%,日本40%)。與(yu) 此同時,美德日三國企業(ye) 對智能製造的悲觀程度的比例均呈現上升態勢,而中國企業(ye) 恰恰相反,持悲觀態度的比例由15%降至11%。整體(ti) 而言,中國企業(ye) 對第四次工業(ye) 革命滿懷信心,對投身智能製造樂(le) 觀而不遲疑。美國和德國企業(ye) 普遍感受到的是迷茫和不確定。日本是企業(ye) 智能製造信心指數始終未能過半的唯一國家(2017年僅(jin) 有40%的日本企業(ye) 對技術革命抱以樂(le) 觀態度)。
做到:中國企業(ye) 走在智能製造應用的最前端
2018年,我們(men) 向全球800多家製造企業(ye) 提出了一個(ge) 新的問題:“貴公司已試點多少個(ge) 智能製造解決(jue) 方案?”結果表明,很多受訪企業(ye) 已經啟動了智能製造用例的試點落地工作。全球範圍內(nei) ,平均每家企業(ye) 已經試行了8個(ge) 數字化製造方案,這是一個(ge) 令人振奮的數字(見圖2)。
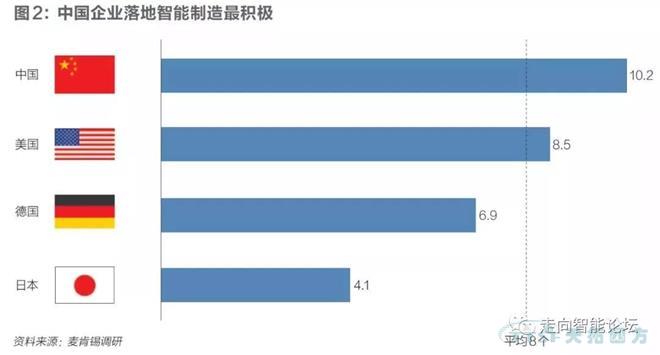
態度決(jue) 定行動,聚焦中美德日四國, 一兩(liang) 年前各國企業(ye) 樂(le) 觀程度和各國企業(ye) 實施方案數量呈正相關(guan) :中國企業(ye) 走在智能製造“做到”的最前端,平均每家中國企業(ye) 已經試點了10.2個(ge) 數字化製造用例,美企平均8.5個(ge) 用例,德企平均6.9個(ge) 用例,日企平均4.1個(ge) 數字化生產(chan) 用例,僅(jin) 為(wei) 全球基準的一半水平。可見在智能製造落地階段,日本遠遠落後於(yu) 中美德三國。
得到:德企和美企仍為(wei) 智能製造的全球領軍(jun) 者,中國企業(ye) 正快速追趕
2018年麥肯錫這份調研報告還顯示,這800多家企業(ye) 中超過70%的企業(ye) 落入了數字化轉型試點“陷阱”,小規模試點之後無法實現公司及生態係統的全麵轉型。企業(ye) 試點進展也十分緩慢。約29%的受訪企業(ye) 表示其試點期已超過兩(liang) 年, 56%表示已進行了一至兩(liang) 年的試點, 15%表示剛剛步入試點階段。
隻有以點及線,以線及鏈,從(cong) 試點走向規模化,才能獲取智能製造的最大價(jia) 值。2018年5月起,麥肯錫與(yu) 世界經濟論壇(WEF)聯手,在全球範圍內(nei) 遴選智能製造領域的“得到”者——工業(ye) 4.0“燈塔工廠”。意在總結先行者的成功經驗,惠及製造業(ye) 全球生態圈。最後,我們(men) 在全球約1000家企業(ye) 中選出了16家“燈塔工廠”,它們(men) 分布在製造業(ye) 的各個(ge) 行業(ye) ,數字化試點之後,成功推廣到企業(ye) 整個(ge) 層麵,取得了顯著的財務和運營實際效益(見圖3)。
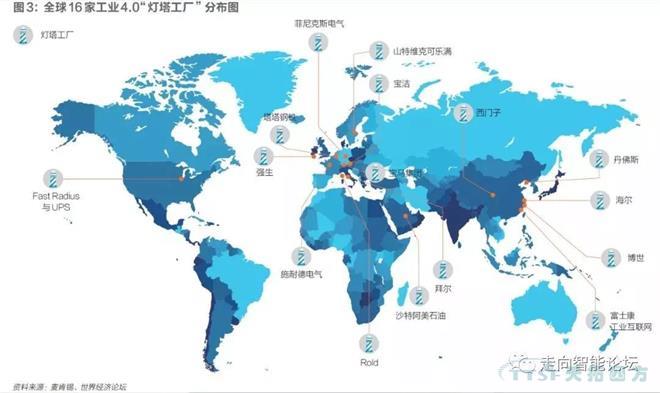
這16家“燈塔工廠”之中,有5家來自德資企業(ye) ,3家來自美資企業(ye) 。作為(wei) 高端製造業(ye) 代表的德國和全球科技創新中心的美國,深厚的先進工業(ye) 底蘊和全麵的高質量生產(chan) 能力奠定了先發優(you) 勢。難能可貴的是,作為(wei) 製造業(ye) 後起之秀的中國,也貢獻了2家“燈塔工廠”(海爾和富士康),且坐標在中國的“燈塔工廠”有5家(海爾、富士康、西門子、博世和丹佛斯),全球最多。“中國製造”第一次成為(wei) 智能製造的全球標杆,也是發展中國家第一次在世界製造業(ye) 領跑軍(jun) 團中占據了一席之地。
2015年以來,工信部陸續選出305個(ge) 智能製造試點示範項目,形成了各地各行各業(ye) 的中國版“燈塔”。這些智能製造試點示範項目,涉及92個(ge) 行業(ye) 類別,覆蓋全國境內(nei) 所有省(自治區、直轄市),拉動投資超過千億(yi) 元人民幣。初步統計,這些項目智能化改造前後對比,生產(chan) 效率平均提升37.6%,最高提升了300%。
多方合力、共推智造
2019年5月8日,筆者在日本東(dong) 京與(yu) 100多名日本企業(ye) 高管就數字化轉型開展了一場深度交流。超過三分之二的日本高管坦承其所在企業(ye) 已經落後於(yu) 全球工業(ye) 互聯網的革新步伐。但反差的是,他們(men) 普遍認為(wei) ,在落地數字化用例之前,必須對方案設計、難度估判、投資回報率計算做好充分準備。日本企業(ye) 家們(men) 恪守著謹慎、實用的行事原則,這也正是日本民族文化的縮影。
我們(men) 長期觀察日本企業(ye) 的轉型發現,“同而大和”的集體(ti) 性格深深烙在組織的每一個(ge) 細胞。“同”是先決(jue) 條件,任何變革都須取得自上而下的全體(ti) 認同,這是一個(ge) 漫長而反複的過程。“大和”則是加速器,一旦勠力同心,轉型落地就會(hui) 獲得上層的強力支持和基層的踏實執行。與(yu) 中國對於(yu) 智能製造“因為(wei) 相信、所以看見”有所不同,日本對於(yu) 智能製造則是“因為(wei) 看見、所以相信”。
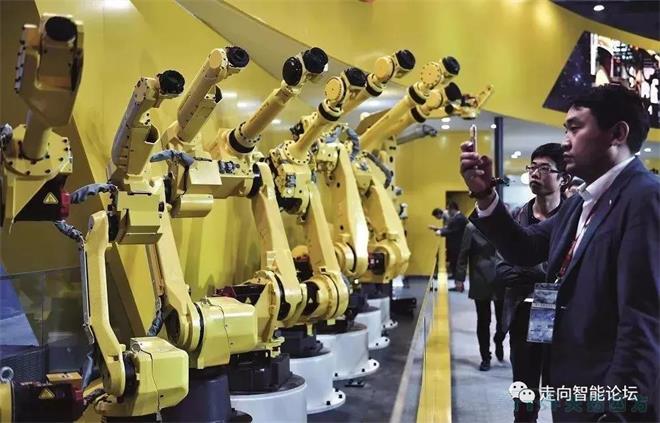
(機器人製造巨頭之一日本發那科公司的機器人係列。圖/ 視覺中國)
從(cong) 日本到德國跨越七個(ge) 時區,筆者來到萊茵河畔一家製造企業(ye) ,主持了一場精益和數字化轉型效率推進研討會(hui) 。除了管理層外,主辦方還邀請了幾位一線生產(chan) 管理人員。
令筆者印象最深的是一位叫奧利弗的裝配線生產(chan) 主管。老奧利弗今年55歲,在車間摸爬滾打了30多年,是名副其實的生產(chan) “萬(wan) 事通”。當我們(men) 在討論是否應該引入穿戴式設備、室內(nei) 定位和RFID技術,為(wei) 車間生產(chan) 員工效率數字化賦能時,奧利弗起身表示有話要說。
他說智能製造也許不是目前這家工廠最合適的出路。原因有三個(ge) 。第一,數字化的意義(yi) 不明顯。這家工廠並沒有任何標準操作手冊(ce) ,奧利弗和他的200多位生產(chan) 夥(huo) 伴在過去的二三十年間,早已熟稔了裝配步驟、產(chan) 品參數、設備狀況的每一個(ge) 細節。工人們(men) 在這家工廠都一二十年了,穩定的員工隊伍和始終如一的重視質量,形成了由工人主導的生產(chan) 質量管理體(ti) 係。數字化工具導入不見得讓這些老兵做得更好。
第二,政策法規對個(ge) 人隱私的保護趨於(yu) 嚴(yan) 格。數字化應用需要獲取一線工人的數據,歐盟最近通過的個(ge) 人數據保護條例要求每一次數據采集都須征得本人同意,這在歐洲國家幾乎是不可能實現的。
第三,數字化的投資回報率不明確。大多數德國工廠隻運行一個(ge) 班次,現在工會(hui) 還在討論將周工時進一步削減,有限的生產(chan) 資源已無法支撐數字化應用的試點性效益落地,遑論組織整體(ti) 的數字化轉型。
德國的製造業(ye) 改革複興(xing) 掣肘於(yu) 發達國家所固有的意識形態和製度法則。激進、徹底、速贏的改革舉(ju) 措很難得到德國製造從(cong) 業(ye) 者的歡迎,德國需要的是合適、合理、合規的做法。
合適是適應德國低離職率、以人為(wei) 本的製造現狀,為(wei) 基層工人提供更加便利友好的生產(chan) 環境;合理是以質量、生產(chan) 率、運營成本為(wei) 目標,科學優(you) 化整個(ge) 製造過程;合規是確保企業(ye) 轉型契合國家的法治精神。智能製造在德國,需要仔細思考技術與(yu) 人、技術與(yu) 製造係統、技術與(yu) 法律的可持續關(guan) 係。
中國是當今世界最大的改革試驗田,我們(men) 可以看到中國製造業(ye) 的今天和明天。
中國製造業(ye) 的今天,近30年的人口紅利期即將結束,勞動力成本和人口老齡化形成上升雙擊,大量勞動密集型產(chan) 業(ye) 麵臨(lin) “用工貴”和“用工荒”的嚴(yan) 峻形勢。
某製造業(ye) 台企董事長曾向筆者吐露了他“想退休但不能退”的無奈心聲。他在大陸的工廠有6000多名員工,但近年來飽受勞動力短缺的困擾。其大陸工廠員工平均工齡不足6個(ge) 月,工人離職率居高不下;工廠所在地區工資水平不斷攀升,原有報酬根本無法吸引現在年輕人;企業(ye) 的自動化程度很低,大多數流程極度依賴熟練操作工人;加上不斷老齡化的中國社會(hui) ,未來工廠甚至將出現操作工的斷代風險。
企業(ye) 招工難,進而導致產(chan) 能波動和產(chan) 品質量問題。言及至此,年逾七旬的老者幾近哽咽。
中國製造業(ye) 的明天,關(guan) 鍵利益相關(guan) 者直麵中國製造業(ye) 當前的勞動力挑戰,以開放的姿態擁抱創新場景,凝聚多方能量形成合力,四股力量推動中國製造業(ye) 涅槃重生。
第一股力量來自對於(yu) 數字化持開放態度的員工。與(yu) 發達國家不同,中國一線員工對智能製造新興(xing) 技術更顯樂(le) 觀。廣大的基層工人積極接納與(yu) 學習(xi) 數字化工具,為(wei) 轉型落地奠定了能力基礎。
第二股力量來自對於(yu) 規模化效益滿懷預期的業(ye) 務領導者。統帥轉型的業(ye) 務負責人認同中國製造規模大,普遍采用三班生產(chan) ,因此智能製造投資回報快。
第三股力量來自偏好新工廠的技術供應商。中國本土的技術供應商將以突破性技術重塑工廠為(wei) 己任,致力於(yu) 優(you) 先開發數字化應用,為(wei) 轉型推廣提供了技術支撐。
第四股力量,來自大力支持的政府部門。2018年,富士康新成立的工業(ye) 互聯網創新企業(ye) 工業(ye) 富聯,從(cong) 提交材料到上市過會(hui) 僅(jin) 用了36天,締造了A股市場IPO的最快速度。政府對於(yu) 智能製造的壯誌雄心和鼎力支持是最核心的推動力。
放眼中國,越來越多的製造企業(ye) 紛紛采用物聯網、人工智能、新一代自動化等工業(ye) 4.0突破性技術。筆者走訪過在中國的五家“燈塔工廠”,它們(men) 比歐美同行更重視與(yu) 人員相關(guan) 的數字化和自動化技術導入,旨在提升製造人員效率,提高產(chan) 品質量。在海爾的青島中央空調工廠,實時數字化業(ye) 績管理將員工的當班業(ye) 績與(yu) 個(ge) 人獎金實時掛鉤;在無錫博世的生產(chan) 現場,新落成的數字技能培訓中心為(wei) 智能生產(chan) 線培育新一代“智能製造者”;在天津丹佛斯的質檢工位,基於(yu) 人工智能機器視覺的檢驗係統,以零誤差率完成每一次高精度的部件質量檢驗。采用智能製造技術,不讓供不應求的一線生產(chan) 人員做不喜歡、不擅長、不安全的工作,而讓他們(men) 做更有價(jia) 值的工作,是多方合力下的明智之舉(ju) 。
中國智能製造不能等,要兼容並蓄、集之大成
中國的智能製造在快速追趕,但製造業(ye) 整體(ti) 大而不強的現狀還遠未改寫(xie) 。如果把智能製造比作一場長跑,那麽(me) 大多數中國企業(ye) 還處在第二、第三軍(jun) 團位置。智能製造是一場非常規的長跑,是一場沒有規定賽道的長跑。筆者相信,選擇賽道是擺在企業(ye) 家麵前的考題,而答案很可能是兼容並蓄,集之大成(見圖4)。與(yu) 我們(men) 同時奔跑的德國、日本和美國,都具備各自的發展優(you) 勢和可取之處。中國唯有潛心汲取其他製造強國的“武功秘籍”,並化為(wei) 自己的“內(nei) 力”,才能後發先至。
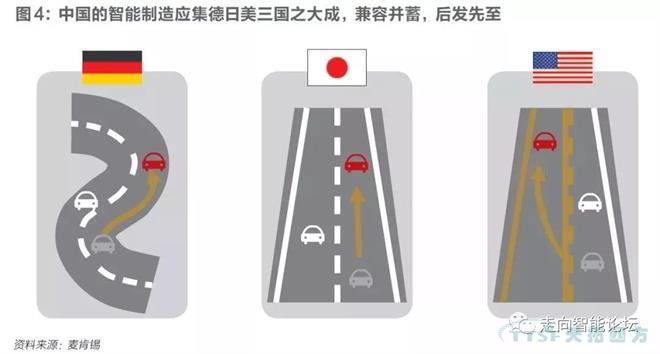
在智能製造的戰略內(nei) 容上,德美日中表現出不同的目的和利益側(ce) 重。德國智能製造戰略:工業(ye) 4.0,目的是發揮其傳(chuan) 統的裝備設計和製造優(you) 勢,進一步提升產(chan) 品市場競爭(zheng) 力和配套價(jia) 值,主要關(guan) 注智能化生產(chan) 製造能力。美國的智能製造戰略:工業(ye) 互聯網目的是發揮其傳(chuan) 統信息產(chan) 業(ye) 優(you) 勢,進一步提升麵向終端用戶的體(ti) 係性服務能力,主要關(guan) 注智能化體(ti) 係服務能力及顧客價(jia) 值創造。日本的智能製造戰略:工業(ye) 價(jia) 值鏈計劃,目的是配合機器人和物聯網,成為(wei) 推進製造業(ye) 升級的三大支柱,主要關(guan) 注尋求建立一個(ge) 生態係統,讓全行業(ye) 所有企業(ye) 共同受益。中國的智能製造戰略:從(cong) 製造大國成為(wei) 製造強國,提升產(chan) 品質量和品牌價(jia) 值,主要關(guan) 注通過形成以智能製造為(wei) 核心戰略的生產(chan) 企業(ye) ,進而帶動相關(guan) 設備和服務研發公司。發達國家向智能製造前進的不同方式,為(wei) 中國智能製造突圍提供了諸多啟示,筆者歸納為(wei) 彎道超車、直道超車和換道超車三種策略。
彎道超車:向德國學習(xi) 根基紮實的智能製造
德國的高端工業(ye) 裝備和自動化生產(chan) 線是舉(ju) 世聞名的,在裝備製造業(ye) 享有傲視群雄的地位。同時,德國人嚴(yan) 謹務實的風格,理論研究與(yu) 工業(ye) 應用的結合也最緊密。可以說德國智能製造的核心競爭(zheng) 力是先進設備和生產(chan) 係統。在德國工業(ye) 4.0的戰略框架中最重要的詞是“整合”,包括縱向整合、橫向整合及端到端整合,從(cong) 而將德國在製造體(ti) 係所積累的知識資產(chan) 集成為(wei) 一套最佳的設備和生產(chan) 係統解決(jue) 方案,通過不斷優(you) 化的生產(chan) 效率和效益實現領先。我們(men) 向德國學習(xi) ,學的就是“彎道超車”,即打造智能生產(chan) 係統解決(jue) 方案。
西門子在成都的“燈塔工廠”就是範例。
2013年,西門子在成都建設的數字化工廠一期,從(cong) 製造流程、產(chan) 線布局、生產(chan) 設備到工業(ye) 軟件執行全麵解決(jue) 方案是其對德國姐妹工廠的複製,由外籍專(zhuan) 家全程指導並統率決(jue) 策,通過一對一緊密指導培育技能,旨在將最純正的德係智能設備和生產(chan) 係統帶到中國,為(wei) 智能製造最佳實踐的本土化創造先決(jue) 條件。時隔五年,其數字化工廠二期啟動,智能製造解決(jue) 方案采用“全華班”配置。100%本土工程師設計和項目管理,本土係統集成商承接項目。由於(yu) 更緊密地融入了本地生態係統,項目僅(jin) 用六個(ge) 月就完成了設計和落地全過程,勞動生產(chan) 率大幅提升,投資回報期非常短。在同一片熱土上, “德國質量”和“中國速度”交相輝映。
直道超車:向日本學習(xi) 智能產(chan) 品的客戶價(jia) 值實現
在日本的製造文化裏,人的價(jia) 值最重要,對人的信任遠勝於(yu) 對設備、數據和係統的信任,所有的自動化、數字化、智能化也都是基於(yu) 如何幫助人更好地工作為(wei) 目的。因而在智能製造領域,日本企業(ye) 談論的不是機器換人或無人工廠,更加關(guan) 注的是在人的工作中嵌入智能產(chan) 品的微觀價(jia) 值。其相關(guan) 研發的主要精力集中於(yu) 產(chan) 品的IoT化和人工智能應用,識別工業(ye) 互聯網各行業(ye) 各價(jia) 值節點的用戶痛點與(yu) 訴求,專(zhuan) 研能夠解決(jue) 現場問題、創造業(ye) 務新價(jia) 值的“點狀”產(chan) 品。向日本學習(xi) ,學的就是“直道超車”,即以用戶為(wei) 中心打磨智能產(chan) 品,用務實的工匠精神提供用戶所需要的實際功能。
基恩士是全世界最好的機器視覺企業(ye) 之一,也是日本以工匠專(zhuan) 研精神塑造智能產(chan) 品的縮影。基恩士是全球率先提供人工智能機器識別技術的企業(ye) ,這源自其對於(yu) 客戶業(ye) 務痛點與(yu) 核心需求的長期關(guan) 注。基恩士認識到隻有人工智能視覺產(chan) 品才能從(cong) 根本上解決(jue) 現有問題,取得行業(ye) 定價(jia) 權。於(yu) 是大力投入研發,依據用戶實際場景度身定製了人工智能及物聯網功能模塊,推出了新一代視覺解決(jue) 方案。該產(chan) 品以其獨有的技術解決(jue) 了其他產(chan) 品無法解決(jue) 的現場問題,牢牢占據機器視覺高端高利潤。2018年,基恩士在中國市場的收入是第二名的近五倍,常年維持70%左右的毛利率。增長的背後就是工匠精神孕育的智能產(chan) 品價(jia) 值。
換道超車:向美國學習(xi) 數據和平台驅動的智能服務
作為(wei) 第三次技術革命的發源地,美國在信息技術領域的積累深厚,擁有全世界最頂尖的信息技術企業(ye) 和研發團隊。因此,在智能製造誕生伊始,美國就提出了“工業(ye) 互聯網”的概念,將數據的整合和使用作為(wei) 戰略重點,通過製定通用的工業(ye) 互聯網標準,利用互聯網激活傳(chuan) 統的生產(chan) 製造過程,促進物理世界和信息世界的融合。
美國智能製造的核心是充分挖掘數據的價(jia) 值,即利用其在大數據、芯片、物聯網、人工智能等“軟服務”上的強大實力,實現真正的工廠智能化,典型用例包括數字化資產(chan) 管理、預見性維護、數字化業(ye) 績管理等。向美國學習(xi) ,學的就是“換道超車”,建立數據采集、傳(chuan) 輸、管理、分析及應用的物聯網架構,用數據驅動工業(ye) 智能服務的模式創新,成就企業(ye) 主業(ye) 以外的新賽道——新興(xing) 業(ye) 務增長點。
總體(ti) 而言,中國製造業(ye) 並沒有如德國等發達國家那樣由第三次工業(ye) 革命逐漸過渡到第四次工業(ye) 革命。中國雖然製造業(ye) 規模最大,但是行業(ye) 水平參差不齊,很多中國企業(ye) 仍處於(yu) 工業(ye) 2.0,甚至更低的水平。同時,種種挑戰也給中國製造業(ye) 的前路帶來隱憂。但是,中國製造的強國之夢並不遙遠。敏而好學、兼容並蓄是中國智慧;勤於(yu) 奮鬥、後發先至是“中國速度”;脫虛向實、萬(wan) 眾(zhong) 創新是“中國創造”。我們(men) 堅信,中國製造業(ye) 的高質量發展將會(hui) 創造下一個(ge) 中國奇跡。