隨著技術創新、客戶需求以及外部環境因素的加速變化,數字化技術和製造業(ye) 的結合越來越緊密,製造業(ye) 企業(ye) 的數字化轉型也正在加速推進。
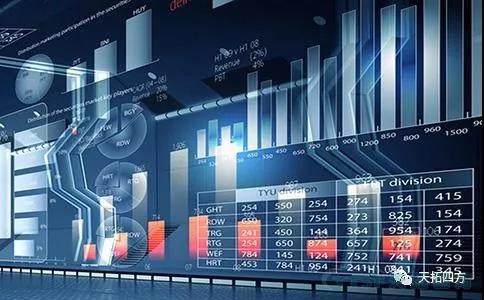
中國中小型製造業(ye) 企業(ye) 在過去幾十年的發展過程中成長迅猛,對數字化的需求越來越旺盛,隨著公司規模的不斷擴展,他們(men) 對IT&OT的需求也越來越多,特別是在新技術的驅動下,中小企業(ye) 的數字化轉型需求同樣勢不可當。不過,必須承認的是相比於(yu) 大企業(ye) ,中小型製造業(ye) 企業(ye) 在人才、資金、技術與(yu) 管理等方麵都較為(wei) 落後,中小企業(ye) 由於(yu) 其業(ye) 務特性導致了其對數字化轉型缺乏緊迫感,數字化轉型經驗相對不足,沒有樹立相對科學的轉型升級體(ti) 係方法論,不能夠相對精準把握數字化轉型的核心要素和戰略取舍。
數字時代的到來,已是社會(hui) 經濟發展中不可逆轉的一種趨勢,所以,本文通過一個(ge) 實際案例,指出中小型製造業(ye) 企業(ye) 如何善用新的變化形式來革新管理理念、手段與(yu) 結構,進一步推動可持續發展,實現數字化轉型升級。
如何以更低的IT&OT成本搭建完整的按需管理方案?如何推動業(ye) 務增長、實現卓越運營?如何通過工業(ye) 互聯網管理關(guan) 鍵的業(ye) 務流程?其他關(guan) 鍵業(ye) 務如何實現數字化管理?
下麵我們(men) 就通過以下案例幫助大家解決(jue) 以上問題。
A公司數字化轉型實例
以下用A公司來代表案例企業(ye) ,A公司是一家生產(chan) 低壓電氣係列產(chan) 品,集科研、製造、加工、貿易於(yu) 一體(ti) 的多元化科技型中小型企業(ye) ,為(wei) 實現新時期的轉型、提升未來的綜合競爭(zheng) 力,擬建立數字化工廠。但“數字化工廠”建設是一個(ge) 龐大、複雜的係統工程,需要按照“總體(ti) 規劃、分步實施”的原則,做好頂層設計,對工程的建設目標、內(nei) 容及建設步驟、優(you) 先級等進行詳細的規劃。
A公司的數字化轉型路徑,遵循精益生產(chan) (Lean Production)的思想,結合業(ye) 界的相對最佳實踐進行對標,構造出針對數字化企業(ye) 的評估體(ti) 係,同時整合匯總A公司的企業(ye) 戰略目標,通過價(jia) 值流分析,得出實現均衡化生產(chan) 、現場可視化管理的策略及具體(ti) 措施,應用仿真技術實現設計、工藝、生產(chan) 一體(ti) 化並建立持續改進機製,提出新工廠布局的初步方案並對現有工藝進行優(you) 化。篩選自動化實施點並提出自動化集成的實施建議,梳理信息化應用構架並提出信息化集成的實施路線圖,最後得出信息化集成、自動化集成、軟硬件選型、實施計劃關(guan) 鍵行動項等內(nei) 容。下麵將針對A公司數字化轉型的核心要素步驟一一展開說明。
步驟一:企業(ye) 數字化現狀評估
數字化企業(ye) 是現代企業(ye) 運行的一種新模式。它將信息技術、現代管理技術和製造技術相結合,並應用到企業(ye) 產(chan) 品生命周期全過程和企業(ye) 運行管理的各個(ge) 環節,實現產(chan) 品設計製造、企業(ye) 管理、生產(chan) 控製過程以及製造裝備的數字化和集成化,提升企業(ye) 產(chan) 品開發能力、經營管理水平和生產(chan) 製造能力,從(cong) 而提高企業(ye) 綜合競爭(zheng) 能力。
數字化企業(ye) 的建設,其最終目的不僅(jin) 是要提高經濟效益與(yu) 資源利用效率,還要提高企業(ye) 的非經濟效益,增強研發創新能力,提高人員素質,改善業(ye) 務流程等。這種多重性決(jue) 定了選擇評估方法時,應采用多指標的綜合評價(jia) ,進行全方位的考核與(yu) 評估。基於(yu) 以上原則,參考德國機械設備製造業(ye) 聯合會(hui) (VDMA)的“工業(ye) 4.0成熟度評測”,我們(men) 製定了數字化企業(ye) 評估範圍。
步驟二:精益生產(chan) 與(yu) 工藝優(you) 化
為(wei) 深入了解生產(chan) 過程的現狀,在數字化轉型規劃期的起始階段,我們(men) 對A公司的現有價(jia) 值流進行了係統的分析,覆蓋到全部工序環節,收集數據包括每個(ge) 工序的:節拍時間、加工周期、批量大小、在製品數量、換型時間、班次、操作員數量、一次合格率、設備年檢修時間等。基於(yu) 需求和產(chan) 線的設計節拍,主要從(cong) 整體(ti) 的產(chan) 線平衡、生產(chan) 柔性限製、拉動導入、工藝痛點以及數據采集需求五個(ge) 方麵進行改進空間識別,分別有助於(yu) 提高效率減少投資、減少批量限製、縮短製造交付周期、優(you) 化工藝流程以及提高智能化水平。
產(chan) 品未來需求 = 1500萬(wan) /年,可用工作天數:26×11 = 286天,日可用工作時間:8小時,客戶需求節拍 = 0.549秒/極,當前自動線設計節拍:2.4秒。
基於(yu) 上述數據,對當前生產(chan) 的線平衡率進行了分析,基於(yu) 預估的工藝數據,目前產(chan) 線平衡率 = 51.9%,智能化工廠的標準是 85%。線體(ti) 設計節拍2.4秒,未來滿足客戶整體(ti) 需求,需要4.4條線,2.55In延時測試和複校工序的預估節拍沒有滿足線體(ti) 設計的2.4秒設計目標,除了優(you) 化單機的節拍時間,可以考慮增加瓶頸工位的設備匹配數量。在提高平衡率的同時,以最少的線體(ti) 數量和投資,實現最終客戶0.549秒的節拍需求。
針對未來點焊和輔助工序廠內(nei) 自製的計劃,建議實施拉動生產(chan) ,結合在線FQC抽檢改善,可以將首件產(chan) 品的製造周期由基於(yu) 推動模式的4.75天,縮減至約40分鍾。在價(jia) 值流分析的基礎上,我們(men) 對現有工藝流程進行了分析。
步驟三:自動化優(you) 化與(yu) 集成規劃
自動化實施點的篩選基於(yu) 兩(liang) 個(ge) 重要的指標:少人化 & 可實現性。少人化用於(yu) 考察實施自動化後帶來的價(jia) 值,可實現性用於(yu) 考察自動化方案的實現難度。首先應該實施的是價(jia) 值大、實現難度低的點。在對A公司自動化產(chan) 線進行場景描述時,對現有情況進行了詳細的梳理,發現存在如下現狀和問題:
自動化設備替代人工作業(ye) ,替代率高。具備基本的人機交互功能。可以通過HMI麵板等顯示設備狀態,檢測數據等信息。基本能夠滿足批量生產(chan) 的要求。生產(chan) 數據及檢測數據無係統采集。更換產(chan) 品型號時,需要人工去相應設備前改參數。大部分PLC和檢測設備無通信接口,無法組成高速工業(ye) 以太網。產(chan) 品的生產(chan) 和質量信息無法追溯。
自動化優(you) 化與(yu) 集成麵向生產(chan) 自動化和檢測自動化的一體(ti) 化,包括設備的互聯互通、設備與(yu) 信息係統的無縫連接、人機交互的界麵等方麵。為(wei) 有效地完成自動化的集成,在項目中我們(men) 采取了如下步驟:
1)實施點篩選,識別出自動化實施點的優(you) 先級;
2)功能概念描述,對自動化需要完成的功能、操作進行文字描述;
3)數據傳(chuan) 輸與(yu) 控製,分析不同智能體(ti) 之間的信號傳(chuan) 遞及響應;
4)全自動化集成,在工業(ye) 互聯網的基礎上實現設備的互聯並與(yu) 上層應用係統集成;
5)設備選型/供應商評估。
步驟四:信息化優(you) 化與(yu) 集成規劃
在數字化轉型的落地過程中,另一個(ge) 很大的挑戰是單個(ge) 信息係統的優(you) 化以及多個(ge) 信息係統的集成。隨著企業(ye) 的發展,越來越多的信息係統被導入企業(ye) ,而係統間的數據交互、係統與(yu) 流程間的匹配程度、係統構架本身的合理性等問題,向信息化集成提出了挑戰。
為(wei) 應對這一挑戰,近年IT界提出了企業(ye) 構架(EA,Enterprise Architecture)的規劃方法,這是一種從(cong) 企業(ye) 戰略出發去梳理業(ye) 務架構,進一步分析和規劃IT架構,並用於(yu) 指導、規範計算機信息係統建設的理念和方法,是當前數字化工廠、數字化企業(ye) 轉型規劃所采用的一種最佳實踐和方法論。
通過對企業(ye) 架構的分析,在對業(ye) 務戰略和業(ye) 務流程理解的基礎上,對企業(ye) 的信息係統進行總體(ti) 規劃和科學實施,從(cong) 而可以將企業(ye) 的業(ye) 務戰略和業(ye) 務流程與(yu) 具體(ti) 的信息係統緊密地結合起來,為(wei) 企業(ye) 描繪出一個(ge) 未來的數字化企業(ye) 中業(ye) 務、數據、應用和技術互動的藍圖。
業(ye) 務架構框架以價(jia) 值鏈為(wei) 基礎,進行流程的逐級細化,並且定義(yi) 了包括客戶管理、產(chan) 品開發、生產(chan) 製造等主要的業(ye) 務功能和職責,最後以流程為(wei) 主要分析角度,建立業(ye) 務架構框架。本案例以A公司的生產(chan) 製造流程為(wei) 分析範圍,覆蓋前四層的企業(ye) 架構分析(Level-0到Level-3),其目的如下:
第一層(Level-0)看價(jia) 值,識別價(jia) 值鏈視圖
第二層(Level-1)看管理,識別業(ye) 務管理視圖
第三層(Level-2)看流程,識別管理流程圖
第四層(Level-3)看活動,識別活動流程圖
業(ye) 務架構是基於(yu) 戰略決(jue) 定企業(ye) 各組成部分如何運轉的工具,建立了企業(ye) 戰略與(yu) 日常運營之間的關(guan) 聯關(guan) 係。從(cong) 企業(ye) 級視角以一種結構化、層次化的方式描述業(ye) 務流程,它具有以下兩(liang) 種特征:
1、以企業(ye) 級視角描述全局的價(jia) 值鏈
2、采用結構化的方式來組織價(jia) 值鏈到任務步驟的業(ye) 務流程。
A公司的業(ye) 務架構 level 0由三部分不同的流程群體(ti) 組成:
管理流程,確定A公司的戰略發展方向,關(guan) 注公司的優(you) 勢和創造基本的框架。
業(ye) 務流程,直接和客戶相關(guan) ,由所有增值程序來組成,主要關(guan) 注外部客戶的利益。
支持流程,是保證運營的流程。
通過對Leve-0~Level-4層級的業(ye) 務架構梳理,期望達到的目的是:通過對A公司生產(chan) 運作管理現狀和存在的問題進行深入細致分析,提出流程優(you) 化或流程管理的新思想;通過對生產(chan) 流程的梳理、流程優(you) 化、流程固化和流程e化等幾個(ge) 階段的研究,提出解決(jue) 方案和具體(ti) 實施對策,構建生產(chan) 流程優(you) 化模型;采用統一的業(ye) 務流程描述語言和工具,清晰各部門職能,明確責任,解決(jue) 流程不清、運行效率低下的問題;識別生產(chan) 流程中的信息交互、數據交互、數據查詢、數據統計,為(wei) A公司導入MES係統奠定基礎。
基於(yu) 信息化現狀的分析,其中ERP和OA已實施,A公司目前產(chan) 品生命周期管理存在很大的提升空間,該提升將很大程度改善設計向製造的轉化效率,故建議率先實施PLM相關(guan) 的信息係統。
A公司未來的應用架構將包含商業(ye) 智能(BI)、PLM、ERP、MES、SCADA、SCM、QMS、CAPP/MPM、WMS+WCS、企業(ye) 內(nei) 容管理(ECM)等核心業(ye) 務應用係統,也將包含業(ye) 務流程管理(BPM)、項目管理(PM)、客戶關(guan) 係管理(CRM)、人力資源管理(HR)、知識管理(KM)等支撐業(ye) 務應用係統。另一方麵,為(wei) 確保各信息係統的平滑運行,還應建立一套完善的IT治理框架,包括:麵向服務的體(ti) 係構架(SOA)和事件驅動的構架(EDA)、IT流程和IT戰略、IT管理/財務/管控等。
步驟五:數字化轉型路線圖設計
在數字化企業(ye) 轉型規劃項目進展的結尾,我們(men) 根據A公司當前的數字化水平與(yu) 行業(ye) 標杆工廠水平做了對標評估,把A公司的數字化工廠的建設分為(wei) 了三個(ge) 階段,第一階段為(wei) 打造區域行業(ye) 標杆水平,第二階段為(wei) 打造國內(nei) 行業(ye) 標杆水平,第三階段為(wei) 打造國家級製造水平。並且每一個(ge) 階段相關(guan) 的建設活動、主要內(nei) 容、時間進度以及初步投資估算都做了相應的計劃和分析,使企業(ye) 能夠根據自身的資金狀況以及節奏確定詳細的轉型升級路線。
在轉型規劃的過程中,我們(men) 也識別出了一些數字化轉型過程中存在的潛在風險,進入實施期後,規劃組成員應與(yu) 實施團隊、供應商、公司領導層一起,進一步識別可能存在的風險,並尋找到消除、規避、控製風險的策略,確保A公司的數字化轉型平穩進行。
以上案例針對中小製造業(ye) 企業(ye) 實現數字化轉型索要經過的五個(ge) 步驟,當然不僅(jin) 如此,企業(ye) 實現數字化轉型不是一蹴而就的,需要更多技術和環節做支撐,實現數字化轉型任重道遠,讓我們(men) 共同努力,為(wei) 實現智能世界貢獻力量!
免責聲明:文章轉自網絡,由天拓四方推薦閱讀,僅(jin) 用於(yu) 知識傳(chuan) 播