智能製造的概念有些寬泛,對於(yu) 西門子來說,涵蓋了從(cong) “工業(ye) 3.0”到“工業(ye) 4.0”很長的戰線。盡管與(yu) 其他行業(ye) 相比,汽車行業(ye) 在數字化轉型道路上走得更遠,但就目前發展情況來看,仍有很多問題尚需解決(jue) 。首先,汽車行業(ye) 必須轉換思維方式,從(cong) 關(guan) 注“更佳組合”轉向全麵掌控整個(ge) 流程鏈,同時還要考慮工廠的生命周期。隻有這樣才能釋放出工廠尚未挖掘的潛力。此外,我們(men) 還需要理清,在海量的現有數據中哪些是我們(men) 需要的,應該在何時何地使用它們(men) ,以及如何讓這些數據被調用。第三項挑戰是係統有序地執行各項標準,因為(wei) 標準是數字化的基礎。
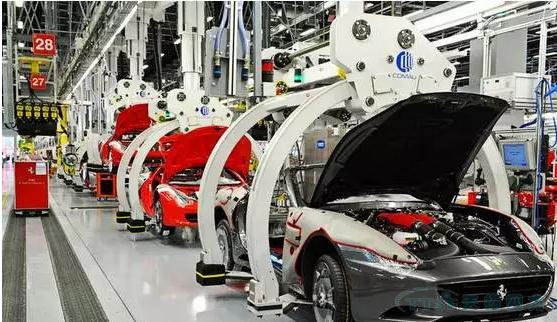
西門子認為(wei) 數字化企業(ye) 是通向“工業(ye) 4.0”和智能製造的必由之路,這一策略需要持續在管理層和員工層普及和培訓,並在財務上予以支持,讓應用工具和企業(ye) 數字化水平同步發展。我們(men) 可以從(cong) 以下六個(ge) 方麵考慮。
管理流程
國內(nei) 車企均尚未製定數字化和自動化總體(ti) 策略和路徑,上汽通用、華晨寶馬、廣汽豐(feng) 田這樣比較先進的合資廠也隻是處於(yu) 起步階段,還沒有完善的策略和路徑。合資企業(ye) 有部分實際的投資金額,本土車企包括新能源車企都還沒有相關(guan) 投資。所有車企均處於(yu) “價(jia) 值鏈上各自獨立的數據庫應用”狀態,無法實現貫穿全價(jia) 值鏈的企業(ye) 級數據協作平台。各自獨立的數據庫造成了新的信息孤島。產(chan) 業(ye) 升級離不開全員素質的提高,特別是管理者的思維認知需要超前一步。大數據方麵,多數企業(ye) 都有各種數據庫,但是應用方麵還很薄弱,部分合資企業(ye) 如上汽通用、華晨寶馬已經開始企業(ye) 大數據的分析工作,上汽通用對CRM數據進行分析,華晨寶馬則已經著手實施大型數據中心的基礎架構建設。
產(chan) 品設計
越來越多的車企已經從(cong) 仿製為(wei) 主轉向了自主正向研發,即便是借助國外設計機構。全三維設計已經是國內(nei) 車企的標配,而要做到多工藝協同對數字化設計軟件的要求更高。產(chan) 品仿真測試的應用已經比較普遍了。產(chan) 品生命周期管理的係統化使用是車企間比較清晰的分水嶺。在產(chan) 品設計階段進行製造工藝文檔的生成和管理,不僅(jin) 提高設計工作的係統性,也為(wei) 後麵生產(chan) 製造環節實現閉環控製提供了可能性。3D打印技術不僅(jin) 使用在概念車型的製作上,將來也會(hui) 大量應用在零配件的製造上。合資車企中優(you) 秀的企業(ye) 已經在做虛擬現實技術的嚐試,如上汽通用已經聘請專(zhuan) 門的虛擬現實設計工程師。
生產(chan) 規劃
在實際產(chan) 品生產(chan) 出來之前,一條虛擬的生產(chan) 線可以幫助工廠進行仿真和優(you) 化。“數字化雙胞胎”概念就好像真實世界在虛擬世界的鏡像,它可以從(cong) 產(chan) 品設計階段一直貫穿到運營服務階段,使得我們(men) 在每一階段的工作都能達到事半功倍的效果。國內(nei) 車企的BOM(Bill of Material,物料清單)係統還處於(yu) 起步階段,目前隻有上汽自主品牌的車型產(chan) 品數據和BOM已實現在企業(ye) 全局的BOM係統中管理。三維的產(chan) 線布置和平衡不僅(jin) 在投產(chan) 的時候才有用,在之後的優(you) 化、調產(chan) 、改造階段能夠節省大量的資源。在生產(chan) 規劃軟件中嵌入變更的追蹤和分析可以使得數據的一致性和效率大大提高。通過對衝(chong) 壓機和機器人係統的仿真,可以在製造單機與(yu) 生產(chan) 線之前模擬出實物,縮短生產(chan) 工期,避免不必要的返工。總裝車間的自動化水平較低,信息化水平滯後,因而大部分車企難以在總裝車間實現虛擬仿真、虛擬裝配與(yu) 人機工程學,一汽和上汽通用也隻能部分實現。在四大工藝日趨成熟的今天,要填補動力總成的研發和質量這塊短板,測試係統不可或缺。
工程實施
一係列自動化創新應用會(hui) 讓企業(ye) 節省大量工作,而統一的標準化的軟硬件和通訊,讓工程數據保持高度一致的同時,並在水平和垂直方向上的集成,進而使企業(ye) 在已有的“工業(ye) 3.0”基礎上又一次騰飛。控製器、分布式 I/O、人機界麵(HMI)、傳(chuan) 動、運動控製係統、電機管理係統等都可以無縫集成到一個(ge) 單一的工程環境。目前隻有上汽大眾(zhong) 和華晨寶馬等少數企業(ye) 能夠貫徹這樣的標準化。企業(ye) 管理水平要提高,統一的標準化文件必不可少。如果將機械設計的過程與(yu) 電氣數據聯係到一起,就可以自動生成PLC程序和相應的E-CAD布局方案。這是工程實施階段跨越性的一步。大部分車企還難以實現自動化設備配置和程序的自動生成,基本處於(yu) 人工編程調試的階段。虛擬調試是自動化技術的革命性突破,在虛擬世界和真實世界之間搭起了橋梁,國內(nei) 已經有少數先行企業(ye) 掌握了這項技術。車企車間內(nei) 以太網一統天下,如果通訊規約統一,會(hui) 讓通訊組態和調試變得更加簡單和迅捷。大數據依賴於(yu) 底層數據的收集,打通垂直數據集成通道是“工業(ye) 4.0”的重要標誌。就目前國內(nei) 所有車企的企業(ye) IT架構現狀,均難以實現垂直數據通道從(cong) 底層自動化感知層直達企業(ye) 管理層。
製造執行
基本的製造管理係統已經成為(wei) 汽車生產(chan) 線中不可缺少的一部分,用於(yu) 收集生產(chan) 線上有關(guan) 設備和質量管理的信息。但是使用的實際效用可以說差距很大。精益製造體(ti) 係的生產(chan) 執行係統在合資車廠中已經基本貫徹,本土車廠也在逐步推行這種理念。公司作業(ye) 過程中文件傳(chuan) 遞電子化的趨勢比較明顯。全自動化的物流設備和係統已經在少數車企實現,下一步是與(yu) 供應商的物流係統對接的時刻。“工業(ye) 4.0”的理想狀態是每時每刻都能夠追蹤產(chan) 品加工狀態,產(chan) 品會(hui) 告訴機器設備,它已經經過幾道工序,現在應該實施哪種工藝。在製造執行階段,係統性地進行物流仿真和產(chan) 能分析屬於(yu) 高階技能。得此技能者得天下。要實現按需生產(chan) ,ERP電子係統必須和消費者/渠道連接在一起。實現這一點還有很長的路要走。
維護服務
汽車製造商想要維持長期的競爭(zheng) 優(you) 勢,更大化工廠的生產(chan) 可靠性和設備綜合效率,同時優(you) 化總體(ti) 擁有成本是關(guan) 鍵的成功因素。將無意義(yi) 的大數據“big data”變身成為(wei) 智慧數據“smart data”,才能利用這些數據製定更加明智的決(jue) 策。不管是新建廠還是老廠,都可以建立三維的工廠模型,這是下一步透明工廠的基礎。透明工廠意味著實時可用的全廠數據流可以在比如說雲(yun) 端用來生成真實工廠的虛擬鏡像工廠,管理者可以隨時調看工廠狀況。戴上VR或者AR眼鏡,整個(ge) 工廠就可以呈現在麵前。
實施問題管理係統,不僅(jin) 要求有經驗的專(zhuan) 家解決(jue) 問題,重要的是要有預案和完善的機製,使得每次問題的出現都能讓我們(men) 找到漏洞和缺陷,讓企業(ye) 運營和管理更上一層樓。
維護服務外包的情況在未來勞動力減少、知識密度提高的趨勢下會(hui) 越來越多。一些企業(ye) 已經實施了能源監控方案,但是還不知道如何利用已經收集的數據。定期維護固然重要,然而預防性維護在提高工廠可靠性上能夠貢獻更多。對工廠裏成千上萬(wan) 的傳(chuan) 感器產(chan) 生的大數據進行挖掘,必然能找出很多可以進一步優(you) 化和改造的機會(hui) ,這也就是所謂的大數據驅動的服務。在這一點上,數據雲(yun) 的應用和發展已經成為(wei) 看得見的未來。
有關(guan) 工業(ye) 信息安全的考慮,合資車企更為(wei) 完善,本土車企在這方麵的意識比較弱,或者說懷著未知的恐慌,而這在未來工業(ye) 智能製造框架內(nei) 占據了重要的位置。