一、案例背景
在當今智能製造蓬勃發展的時代,某大型製造企業(ye) 麵臨(lin) 著優(you) 化生產(chan) 流程、提升設備管理效率以及實時掌控車間生產(chan) 狀況的迫切需求。該企業(ye) 擁有多條自動化生產(chan) 線,分布在麵積廣闊的廠區內(nei) ,各類生產(chan) 設備繁多且來自不同供應商,傳(chuan) 統的人工巡檢與(yu) 分散的數據采集方式已無法滿足精細化管理的要求,急需引入一套先進的物聯網解決(jue) 方案,實現設備互聯互通與(yu) 數據集中管控。
二、網關(guan) 選型與(yu) 部署
經過嚴(yan) 謹的技術評估與(yu) 測試,企業(ye) 選用了天拓四方一款具備高可靠性、強兼容性的工業(ye) 級4G物聯網網關(guan) 。這款網關(guan) 支持4G LTE高速網絡通信,向下兼容3G、2G網絡,確保在複雜的工業(ye) 環境下網絡連接的穩定性,即使在偏遠車間或網絡信號波動區域,也能保障數據傳(chuan) 輸不中斷。
在部署環節,技術團隊依據廠區布局與(yu) 生產(chan) 線分布,將網關(guan) 安裝在靠近設備集中區域的控製櫃內(nei) 。網關(guan) 通過標準工業(ye) 通信接口,如RS485、RS232、以太網口等,與(yu) 各類生產(chan) 設備相連,包括數控機床、PLC控製係統、傳(chuan) 感器等,實現對設備運行數據(如溫度、壓力、轉速、加工參數等)、狀態信息(開機、關(guan) 機、故障報警等)的實時采集。同時,考慮到工業(ye) 現場的電磁幹擾、粉塵、溫濕度變化等惡劣條件,網關(guan) 采用了工業(ye) 級防護設計,堅固的金屬外殼、寬溫工作範圍以及良好的電磁兼容性,有效抵禦外界不利因素,穩定運行。
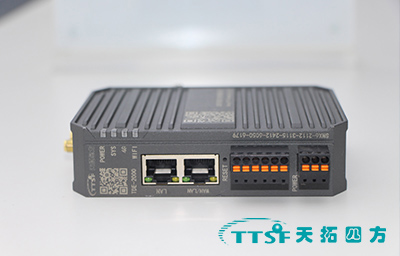
三、功能實現
(一)設備遠程監控
借助工業(ye) 級4G物聯網網關(guan) ,企業(ye) 搭建起了遠程監控中心。運維人員在監控室內(nei) ,通過配套的監控軟件,即可實時查看分布在各車間的設備運行狀況。一旦設備出現異常,如某台數控機床主軸溫度過高,網關(guan) 迅速將報警信息通過4G網絡推送至監控中心,係統自動彈窗提示,並以短信形式通知相關(guan) 責任人,運維人員可第一時間遠程診斷問題,及時安排維修,避免因設備故障導致的生產(chan) 線停工,大幅提升了生產(chan) 連續性。
(二)數據采集與(yu) 分析
網關(guan) 持續采集海量設備數據,並上傳(chuan) 至企業(ye) 私有雲(yun) 平台。數據工程師利用大數據分析工具,對這些長期積累的數據進行深度挖掘。例如,通過分析不同時段設備的能耗數據,結合生產(chan) 任務量,發現部分設備在夜間低穀電價(jia) 時段利用率不足,為(wei) 企業(ye) 製定錯峰生產(chan) 計劃提供依據,有效降低了用電成本;又如,對設備故障前後的運行參數變化趨勢進行建模分析,提前預測潛在故障風險,實現預防性維護,將設備平均故障間隔時間延長了30%。
(三)遠程程序升級與(yu) 配置
對於(yu) 車間內(nei) 的PLC等可編程設備,以往升級程序需要技術人員攜帶電腦到現場逐一操作,耗時費力且易出錯。如今,利用工業(ye) 級4G物聯網網關(guan) 的遠程透傳(chuan) 功能,工程師在辦公室即可將新編程序通過4G網絡遠程下發至目標設備,實現批量快速升級。同時,還能遠程調整設備的配置參數,如修改傳(chuan) 感器采集頻率、控製邏輯閾值等,靈活適應生產(chan) 工藝的動態變化,極大提高了生產(chan) 調整的敏捷性。
四、效益評估
(一)生產(chan) 效率提升
通過實時設備監控與(yu) 快速故障響應,生產(chan) 線停工時間顯著減少,整體(ti) 生產(chan) 效率較之前提升了15%。原本因設備突發故障導致的平均每月20小時停工時間,降低至5小時以內(nei) ,產(chan) 能得到充分釋放,為(wei) 企業(ye) 創造了更多經濟效益。
(二)成本節約
一方麵,預防性維護的推行降低了設備維修成本,每年節省維修費用約30萬(wan) 元;另一方麵,基於(yu) 數據驅動的能耗優(you) 化使企業(ye) 電費支出每月減少5萬(wan) 元左右。此外,遠程運維模式減少了現場技術人員的巡檢工作量,人力成本得以有效控製。
(三)管理精細化
企業(ye) 管理層借助物聯網平台積累的數據,能夠精準掌握生產(chan) 現場的每一個(ge) 環節,為(wei) 決(jue) 策提供詳實依據。從(cong) 生產(chan) 排期優(you) 化到資源調配,管理的精細化程度大幅提升,企業(ye) 競爭(zheng) 力顯著增強。